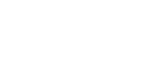
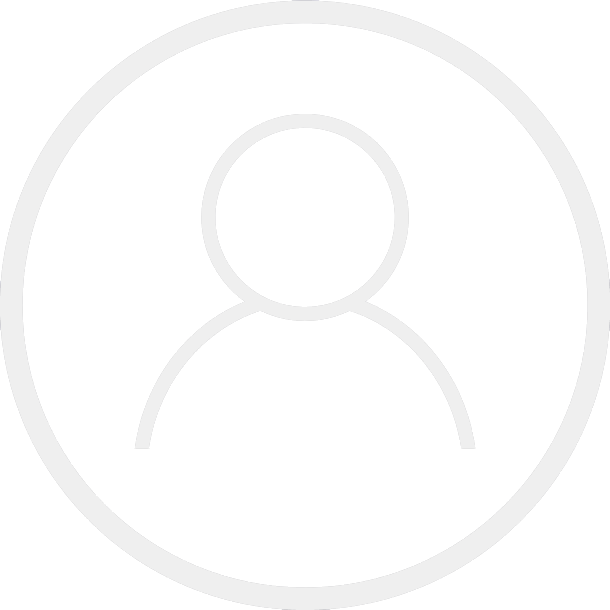
Sign in
New customer? Start here
Cancel
6813C
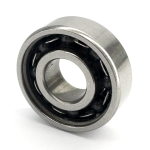
Price $ 21.00
Number
Part Number | 6813C |
System of Measurement | Metric |
Bearing Type | Ball |
For Load Direction | Radial |
Construction | Single Row |
Seal Type | Open |
Bore Dia | 65 mm |
Outer Dia | 85 mm |
Width | 10 mm |
Ring Material | Chrome Steel |
Balls Material | Si3n4 |
Cage Material | 300 Series Stainless Steel |
Dynamic Radial Load | 2675 lbf |
Static Radial Load | 2585 lbf |
Max Speed (X1000 rpm) | 8.6 |
Lubrication | Required |
Temperature Range | -86 to 230 °F |
ABEC Rating | ABEC-1 |
Radial Clearance Trade No | C0 |
Radial Clearance | 0.008mm to 0.028mm |
RoHS | Compliant |
REACH | Compliant |
Weight | 126 g |
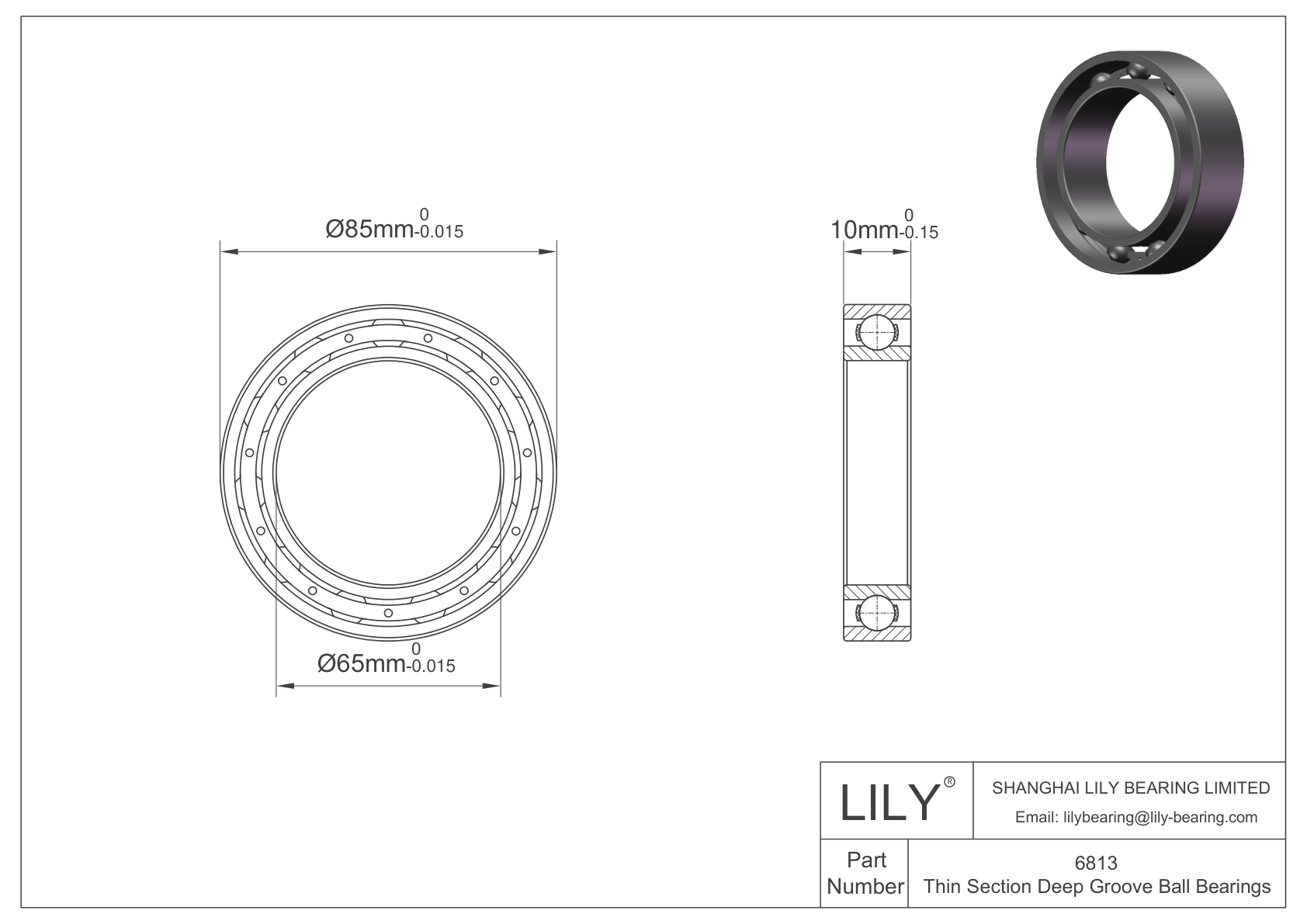
Design Features of 6813C Bearing
6813C Bearing utilizes ceramic balls, typically made of silicon nitride (Si3N4), combined with steel inner and outer races. 6813C bore dia is 65 mm. Its out dia is 85 mm. 6813C width is 10 mm. This Ceramic Ball Bearing provides a sophisticated, high-performance solution that caters to the unique challenges presented by modern industrial and technological applications.
What Benefits Can 6813C Bearing Provide?
- Reduced Friction: Ceramic's low frictional properties ensure smoother operation and decreased heat generation.
- Enhanced Durability: The wear-resistant nature of ceramic extends the bearing's lifespan, particularly in demanding conditions.
- Corrosion Resistance: Ceramic balls resist moisture and chemicals, safeguarding the bearing from corrosive environments.
- Electrical Insulation: Its non-conductive composition prevents electrical arcing, essential in electrically active setups.
- High-Speed Operation: Its attributes permit this bearing to operate efficiently at elevated rotational speeds.
What Can 6813C Bearing Be Used for?
6813C Bearing is employed in various applications due to its unique characteristics. It can be used for:
- Electric Motors: Ideal for preventing electrical arcing, especially in electric vehicles.
- Precision Machinery: Suited for high rotational accuracy needs.
- Aerospace: Meeting the demands of wear resistance and thermal stability.
- High-Frequency Machining: Beneficial for high-speed spindles and machining centers.
- Harsh Environments: Resisting corrosion and withstanding extreme temperatures.